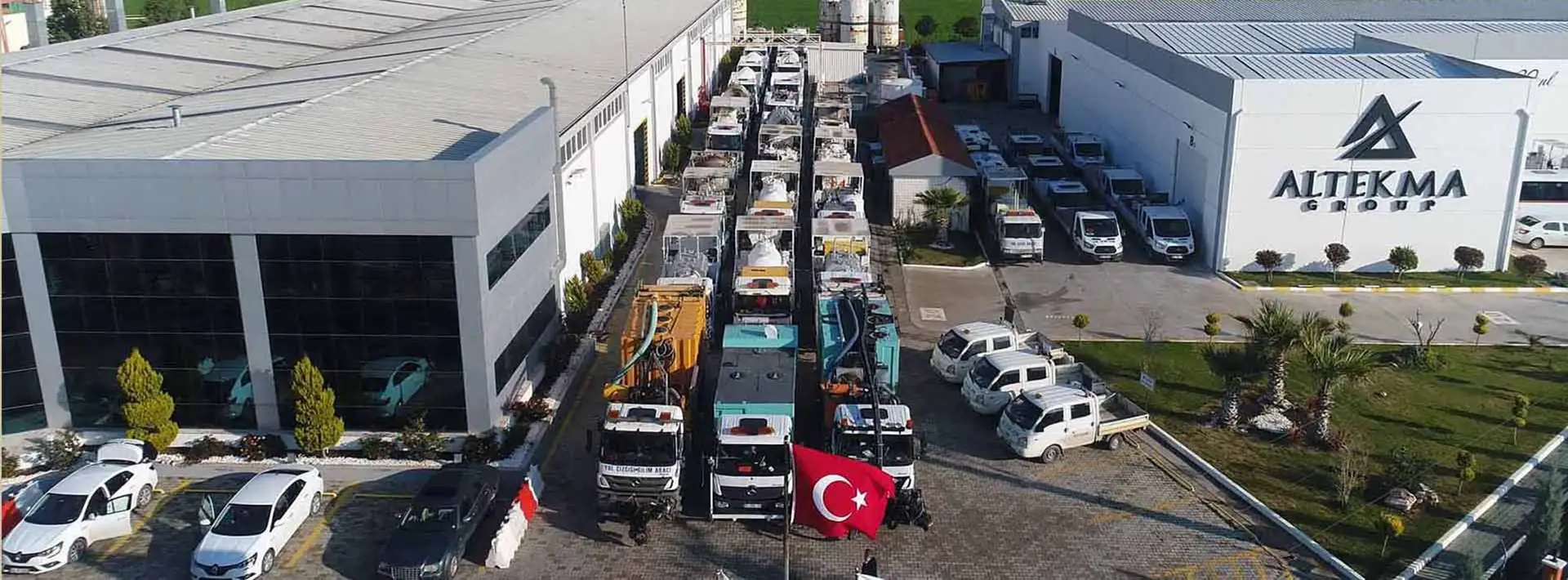
WHAT FACTORS DETERMINE THE TRANSFER EFFICIENCY OF AUTOMATED PAINT SYSTEMS?
WHAT FACTORS DETERMINE THE TRANSFER EFFICIENCY OF AUTOMATED PAINT SYSTEMS?
WHAT IS TRANSFER EFFICIENCY?
When spraying on an object, some of the sprayed material is necessarily sprayed around the object. The term transfer efficiency refers to the amount of material dispensed from the spray gun(s) compared to the amount of paint sprayed onto the object. Transfer efficiency is expressed as a percentage. 60% transfer efficiency means that 60% of the sprayed material actually reaches the target. There was a 40% loss of balance in the spray booth or other areas during the topcoat spraying process.
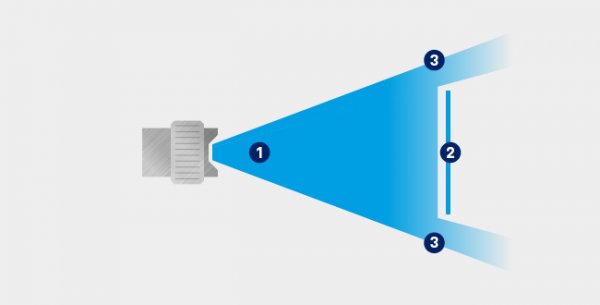
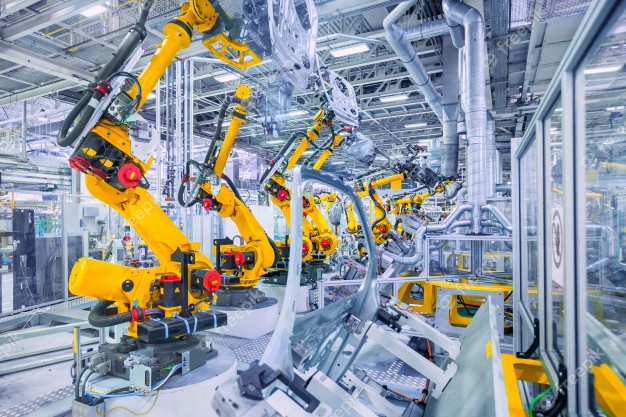
Transfer efficiency = quantity sprayed vs. quantity reaching the target
(1) Liquid (2) Surface (3) Dusting
WHY IS TRANSFER EFFICIENCY IMPORTANT?
By increasing transfer efficiency we reduce paint loss. This leads to a reduction in VOCs released as well as extending the life of your mixing chamber filters. Transfer efficiency can be improved by using different spray applicators. By maximizing transfer efficiency and spraying less paint, manufacturers can save money, reduce the need for maintenance and reduce both filter costs and VOC emissions.
WHAT DETERMINES TRANSFER EFFICIENCY?
The biggest factor in achieving high transfer efficiency is choosing the right spray gun. Choosing the most efficient spray gun for the intended application is important to optimize the efficiency of your spraying process. Traditional air spray, conformal, HVLP, air-assisted, electrostatic and rotary atomizer: all offer great advantages depending on the application.
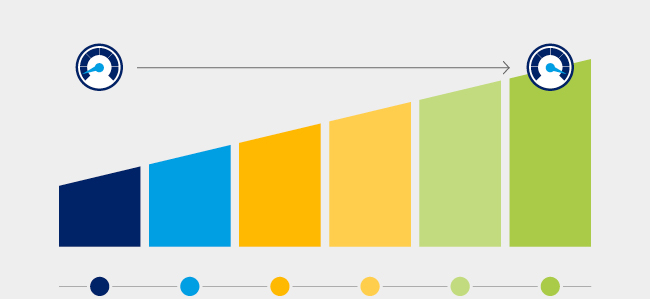
Transfer efficiency
1) Conventional
2) HVLP
3) Airless
4) Air Supported
5) Electrostatic
6) Rotary
In general, each spray technology has its advantages and disadvantages. Determining what the highest requirement is for your production line will help you determine which spray technology will suit your application. Other factors such as operator techniques, proper gun setup, spray mold height, grounding in the spray booth and weather conditions can also affect transfer efficiency.
When spraying on an object, some of the sprayed material is necessarily sprayed around the object. The term transfer efficiency refers to the amount of material dispensed from the spray gun(s) compared to the amount of paint sprayed onto the object. Transfer efficiency is expressed as a percentage. 60% transfer efficiency means that 60% of the sprayed material actually reaches the target. There was a 40% loss of balance in the spray booth or other areas during the topcoat spraying process.
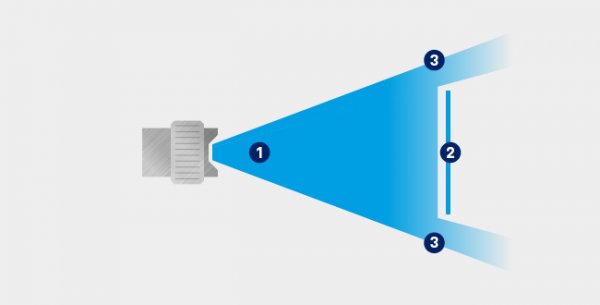
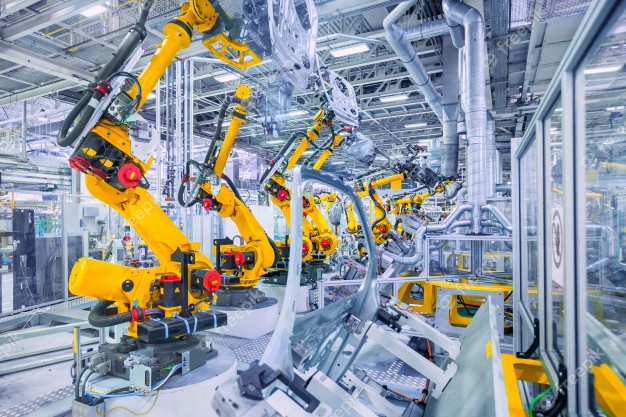
Transfer efficiency = quantity sprayed vs. quantity reaching the target
(1) Liquid (2) Surface (3) Dusting
WHY IS TRANSFER EFFICIENCY IMPORTANT?
By increasing transfer efficiency we reduce paint loss. This leads to a reduction in VOCs released as well as extending the life of your mixing chamber filters. Transfer efficiency can be improved by using different spray applicators. By maximizing transfer efficiency and spraying less paint, manufacturers can save money, reduce the need for maintenance and reduce both filter costs and VOC emissions.
WHAT DETERMINES TRANSFER EFFICIENCY?
The biggest factor in achieving high transfer efficiency is choosing the right spray gun. Choosing the most efficient spray gun for the intended application is important to optimize the efficiency of your spraying process. Traditional air spray, conformal, HVLP, air-assisted, electrostatic and rotary atomizer: all offer great advantages depending on the application.
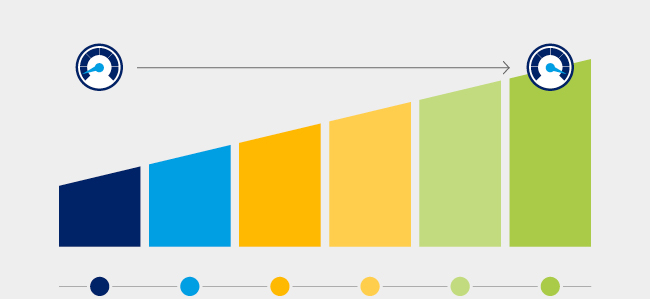
Transfer efficiency
1) Conventional
2) HVLP
3) Airless
4) Air Supported
5) Electrostatic
6) Rotary
In general, each spray technology has its advantages and disadvantages. Determining what the highest requirement is for your production line will help you determine which spray technology will suit your application. Other factors such as operator techniques, proper gun setup, spray mold height, grounding in the spray booth and weather conditions can also affect transfer efficiency.